为充分发挥能效先进企业的带动引领作用,推动工业重点领域能效对标赶超,引导重点用能行业企业创建能效“领跑者”,近日,安徽省经济和信息化厅围绕化工、钢铁、水泥、轮胎等重点行业征集梳理了一批能效提升先进企业典型案例,推进工业领域节能降碳绿色发展。
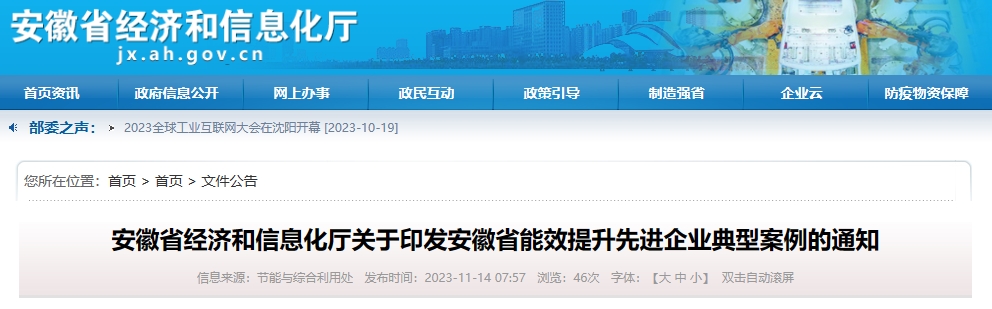
其中包括合肥南方水泥有限公司和天瑞集团萧县水泥有限公司两家水泥企业案例。
合肥南方水泥有限公司
2022年8月至2023年9月,公司6000t/d水泥熟料生产线熟料单位产品综合煤耗为84.07kgce/t,满足1级能耗限额等级要求;熟料单位产品综合电耗为43.57KWh/t,满足1级能耗限额等级要求;熟料单位产品综合能耗为89.44kgce/t,满足1级能耗限额等级要求。依据《工业重点领域能效标杆水平和基准水平(2023年版)》,公司单位熟料能耗水平达到行业标杆水平。到“十四五”末,公司熟料单位产品综合能耗计划降低至81.64kgce/t,减排二氧化碳14.2万吨/年。
先进做法:
(一)开发利用可再生能源
1. 光伏发电:利用物料堆棚、厂区屋顶和熟料库墙壁建设光伏发电设施,其中碲化镉发电玻璃5626㎡ ,装机容量0.58MW,年发电35.63万KWh;单晶硅发电安装面积6109.45㎡,总装机容量1.3 MW,年发电126.86万KWh。
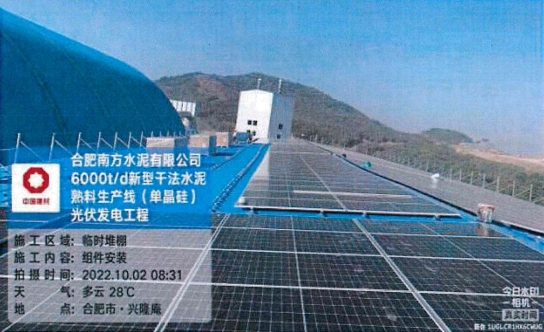
2. 空气能:安装了两套空气源热泵热水系统,分别用于宿舍和食堂,可将水加热至50℃~65℃。
(二)应用先进节能技术工艺装备
1. 使用高效机电设备:公司使用的节能风机均达到1级能效,变压器均为2级能效及以上,电机采用了YE等系列节能电机,比例占70%以上。并对篦冷机冷却风机、窑尾排风机和余热发电循环水泵进行变频改造。
2. 使用节能照明:厂区灯具总计1668个,其中led灯具和太阳能灯具共1408个,节能型照明设施占比60%。
(三)加大节能降碳技术改造力度
1. 新型低碳水泥粉磨技术
通过优化多组分在线可调控制备工艺技术和开发稳态调节进料装置,精准分级和混合材颗粒,实现熟料高效粉磨,节约能耗10%。同时采用高压辊磨机设备和高压力料床粉碎技术,提高系统效率。
2. 高效低碳水泥熟料煅烧技术
提高旋风预热器的分离效率、降低系统阻力,实现六级预热器C1出口负压≤4900Pa等。
3. 耦合煅烧低碳生料制备技术
公司计划在6000t/d的熟料生产线中建设一套360t/d的替代燃料利用系统,实现尾煤30%以上的替代率。项目包括替代燃料的暂存及输送系统,以及辅助生产设施。预计可增加窑产量至8000t/d,平均热值达到4000kcal/kg,尾煤替代率为30%,每天节约213.26t实物煤、减排459.3tCO2。
(四)数字化绿色化协同升级
公司建设数字化全流程生产管控平台,建立工业大数据仓库,实时优化生产管理和辅助决策。实现烧成系统实时优化控制、磨机一键启停自动控制、设备智能运维及健康管理,全面提高企业自动化和生产管理水平,推进精细化管理和精益生产,节能降耗,减污增效。
天瑞集团萧县水泥有限公司
2022年,公司熟料单位产品综合煤耗为89.46kgce/t,满足1级能耗限额等级要求;单位产品综合电耗为48.99KWh/t,满足2级能耗限额等级要求;单位产品综合能耗为95.48kgce/t,满足1级能耗限额等级要求。依据《工业重点领域能效标杆水平和基准水平(2023年版)》,公司单位熟料能耗水平达到行业标杆水平。至“十四五”末,预计全部达到能耗限额1级标准。
先进做法:
(一)开发利用可再生能源
1. 采用生物质燃料替代。糠醛渣、秸秆、木屑等作为生物质能属可再生能源,作为替代燃料用于水泥熟料的生产,可减少煤的用量,同时减少生产中NOx的排放量,具有较好的应用前景。利用生物质替代燃料,预计可替代10%左右的原煤(目前正在试验调试阶段)。
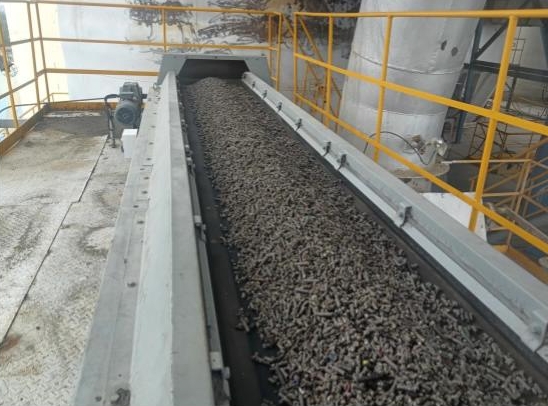
2. 厂区安装了两套空气源热泵热水系统,分别用于宿舍和食堂。该装置消耗1份的电能驱动压缩机运行,同时可从环境空气中吸收转移约4份的热量到水中,可以把水加热至50℃~65℃,满足厂区食堂热水和员工洗浴要求,减少了电热锅炉的使用。
3. 厂区安装了150套太阳能路灯,控制模式为时控,亮灯时间可分时段调整,在细节上利用了可再生能源,降低能源消耗。
(二)应用先进节能技术工艺装备
1. 水泥熟料余热回收中置破碎技术:采用15°固定斜坡篦床和空气炮消除“雪人”现象,预防熟料死区产生。MFR调节器控制冷却风量稳定,小风量阀保障合理分配,降低电耗和煤耗。入料温度1350℃~1450℃,出篦冷机温度降至65℃+环境温度,热回收效率达75%以上,余热回收效率提高8%。
2. 窑尾360°燃烧器节能降碳技术:将分解炉燃烧器改造为喷枪,每根喷枪有28个喷嘴,深入分解炉中心,煤粉雾化后360°无死角喷入炉中。改造后,煤粉燃烧得到平稳合适的空气量,炉空气与燃料增大混合面积,可完全燃烧,降低热力型NOx生成,减少脱硝成本和煤耗成本。喷枪位置布置合理,温度场分布合理,提高了燃尽率和燃烧速度。
(三)高温风机和循环风机节电改造
采用耐磨复合板叶片、中盘护板、进口锥型板等以及特殊设计的风机叶轮,改善出口气流状态,提高工作效率,延长使用寿命并减少涡流。改造后吨熟料节电约2度,每年可节约用电量320多万度,节约标准煤393. 3吨,减少二氧化碳排放1062吨。