在杭州湾畔的嘉兴海盐县,与中国第一座核电站比邻而立,世界最大的单体水泥粉磨企业——海盐秦山南方水泥有限公司依海而立。它用“蓝海战略”点睛之笔,书写“海河联运”创新发展传奇,实现了“公改水”低碳运输。随着自动化、智能化技术的应用,成为长三角地区环保水平最高、综合竞争优势最强的智能化绿色水泥生产基地。
多年来,南方水泥始终牢记习近平总书记重托,开创进取,砥砺前行,坚持以行业供给侧结构性改革为主线,不断通过资源整合、物流整合、优化升级,努力实现企业高质量发展。
推动转型升级,提升企业竞争实力
2016年,为充分发挥嘉兴市海河联运资源的独特优势,优化产业布局,实现嘉兴区域整合优化、技术升级和绿色转型。南方水泥以秦山南方为主体,积极推进浙江省“腾笼换鸟”工作,关停整合嘉兴、嘉善、海盐、桐乡等地9家小、散型粉磨企业,建设集内河、外海运输为一体的现代化粉磨基地,配套12个300吨级泊位的内河码头、2个500吨级内河散装水泥发运系统和2个5000吨级外海码头。并依托南方水泥下属的长兴区域熟料产能、湖州物流内河水运以及海盐港口资源,充分发挥海河联运优势,进一步扩大成本优势和销售辐射范围,实现区域合作、联动发展目标,同时企业实现转型升级和可持续发展。
2018年4月一期项目投产,2021年3月秦山南方海河联运项目建成投产,通过搭建一套全流程生产管理系统,实现了生产效率、节能效率、资源综合利用率的全面提升。升级项目与原有小、散企业相比,腾换土地903亩,节约能耗35.5万吨标煤,人均年劳动生产率从0.7万吨左右,提升到8万吨以上,人均收入稳步增长,实现企业员工双赢,提升企业竞争力。
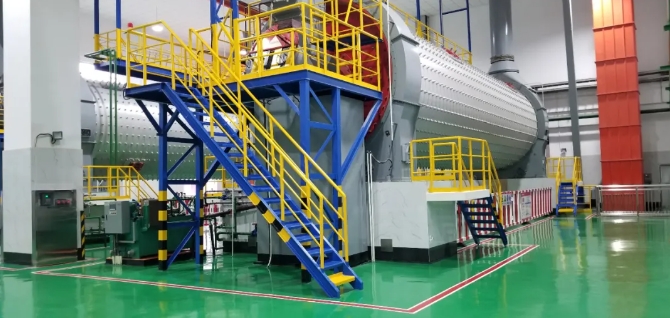
深化三精管理,助推企业提质增效
秦山南方持续深化“三精管理”,做深做实做细,持续创新追求精益求精,全力打好“提质增效”攻坚战。积极推进设备升级改造,水泥磨系统采用辊压机+球磨机双闭路挤压联合粉磨系统,可以在保证产量规模的同时降低粉磨系统单产电耗;辊压机、水泥磨机等设备采用自动化控制系统和变频技术,降低设备能耗;在粉磨过程中,通过加入少量的助磨剂,消除细粉的粘附和聚集现象,加速物料粉磨过程,提高粉磨效率,降低单位粉磨电耗,提高产量。通过智能检测设备、全生命周期设备智能运维平台,基于大数据+AI技术的全流程生产智能控制平台,以及工业互联网双中台的水泥智能制造平台等应用,创新探索出“数据智能为基础、智能维护做保障、智能生产提效益”的智能化生产模式,实现工厂运行自动化、管理可视化。
优化产品结构,赢得市场竞争优势
秦山南方从2020年就提出稳增长、调结构、增效益的市场策略,在产品的研发和生产上,优化品种结构、发挥产线优势,积极增加高标号水泥产品和特殊用途水泥产品的生产比重。淘汰P.O 32.5普通硅酸盐水泥,主打P.O 42.5普通硅酸盐水泥、硅酸盐水泥P.II52.5,以及高铁专供低碱42.5水泥等。通过优选熟料、水泥混合材原料,严格控制原料中碱含量、游离氧化钙等技术手段,外购原材料实行固定矿点签定专项保供等措施,相关质量技术指标、储量、生产保供措施等全面、系统、可控,产品具有强度高,色泽好,抗腐蚀等优点,深受顾客信赖,产品主要销往浙江、江苏、上海及沿海城市。秦山南方多个特种水泥产品销量均取得了较大的市场占有份额,调结构、增效益策略初见成效。
坚持绿色发展,厚植最美生态底色
秦山南方始终贯彻落实习近平生态文明思想,深入践行“两山”理念,走生态优先、绿色发展道路,助推企业快速转型升级。通过规范化改造排放口;封闭外海原料存储四联库库底、熟料装卸船地炕入口等未封闭的位置;建设无组织排放集中管控平台;安装空气质量监测微站、洗扫车安装GPS定位装置、增设符合规范的洗车装置,针对易产尘点设置收尘器165台,实现生产环节全流程无组织排放达标。同时,对粉尘主要排口和厂界安装颗粒物在线监控系统,厂区内安装空气质量检测站实时监测厂区环境空气质量,确保污染物超低排放。有组织废气排放限值由20mg/m3减至10mg/m3,可节约电能350万度,每年可减排二氧化碳约3400吨、二氧化硫约100吨、氮氧化物约50吨、颗粒物约250吨。2022年,秦山南方水泥成功入选嘉兴市“第二批市级绿色园区”,获评“浙江省级绿色低碳工厂”、“浙江省节水标杆企业”、“嘉兴市职业健康示范单位”等称号,秦山南方成为浙江省首批嘉兴市唯一通过超低排放改造验收的企业,是全省首批完成全部超低排放改造工作并通过验收的水泥企业,2023年11月底通过嘉兴市“无废工厂”评审。公司以实际行动切实履行好央企的社会责任,以更好的环境效益回报社会,为生态文明建设做出贡献。
“绿水青山就是金山银山”。秦山南方成功走出了一条供给侧结构性改革转型升级与企业绿色发展之路。在《贺信》的指引下,实现国有资产保值增值,促进效益持续增长,实现高质量绿色发展,为助力南方水泥打造具有中国特色的世界一流企业不断贡献秦山力量。
来源:南方水泥