水泥行业脱硝最大的难点是氨逃逸超标
从2004年开始水泥企业的NOX排放要求<320或400mg/Nm³,同时要求氨气排放小于8或10mg/Nm³,水泥企业通过安装SNCR脱硝以来,NOX排放达到了要求,但氨逃逸远远超过8或10mg/m³(氨逃逸造成窑尾袋除尘器的箱体腐蚀严重)。至今,由于水泥企业没有安装氨逃逸在线监测设备,氨逃逸没有严格执法。
近期中国环科院和部分省环保厅对多个水泥企业采用“精准SNCR”、“炉内还原”和高温高尘SCR脱硝项目进行现场抽样检测,NOX勉强<50或100mg/Nm³,但氨逃逸普遍超过8mg/Nm³,最高达到265mg/Nm³。氨逃逸超标至今还是水泥行业脱硝没有解决的盲区。
SCR脱硝项目氨逃逸原因分析
水泥窑预热器产生的NOx为800~1500mg/Nm³,需要降到出口50mg/Nm³,因此需要采用SNCR+SCR脱除750~1450mg/Nm³的NOx,NOx和NH3的摩尔比是0.37,需要氨气的量为277.5~536.5mg/Nm³,为了实现氨气排放<5或8mg/Nm³,需要准确到将用量的氨气还原消耗97%以上,才能实现氨逃逸不会超标。在预热器内采用SNCR脱硝喷的氨水,只有50%左右的NH3与窑炉烟气的NOx发生还原反应,50%左右的NH3从C1出口逃逸,为了C1出口烟气中的NH3和NOx还原,需要通过SCR反应器进行催化还原。匹配相对应比表面积的催化剂,同时保证烟气中的NH3和NOx在催化剂表面有足够的接触还原时间。由于没有适合高温高尘的高效低阻除尘器,国内水泥企业在2018年开始采用高温高尘SCR脱硝,高温高尘SCR脱硝(一般是采用11孔和13孔催化剂)设置4或5层催化剂,水泥窑预热器C1出口含尘浓度在100~190g/Nm3的粘性生料的烟气直接进催化剂,每小时几十吨生料连续通过几层催化剂,催化剂容易堵塞,催化剂堵塞,严重影响生产,催化剂使用寿命只有3~6个月时间。让水泥企业苦不堪言,如何让SCR脱硝通畅,阻力小,成了第一目标,脱硝效率和氨逃逸达标成了其次,偏离主体,本末倒置。通过采用9孔催化剂、改进催化剂清灰方式和增加催化剂强度,几年的努力下来,高温高尘SCR脱硝的催化剂使用寿命有一定增加,勉强能够保证预热器生产的通风。这样给很多人一个假象:以为高温高尘SCR脱硝在水泥行业成功了。通过案例分析,例如5000吨熟料线,采用高温高尘SCR脱硝时,920000m³/h风量在Φ4.1m管道(管道切面积为13.2㎡)风速是19.3m/s,需要设计的SCR反应器箱体截面积为7*12=84㎡,催化剂采用一层11孔+三层13孔,催化剂280立方,比表面积合计(70*250+70*3*300)=80500平方,按照催化剂72%的开孔率,催化剂孔内有效通风面积为84*72%=60.48㎡,催化剂孔内风速为920000/60.48/3600=4.22m/s,每小时预热器C1出口有超过40吨高温粉尘通过4层催化剂,只要堵塞的催化剂没有超过70%。每一层催化剂通畅孔的面积超过30%即60.48m2*30%=18.14㎡,通风面积超过管道切面积13.2㎡,SCR反应器对预热器生产的影响不大,但催化剂可能有接近70%已经失效了,这时候通畅的催化剂孔内风速为920000/18.14/3600=14.1m/s(催化剂内孔合理风速是3.5~4.5m/s),催化剂磨损严重,使用寿命短,这时候SCR反应器出口氨逃逸一定超标。如果催化剂堵塞超过70%,开始影响预热器生产时,超过70%的催化剂失效,SCR反应器氨逃逸更加超标,通畅的催化剂孔内风速超过14.1m/s,催化剂磨损严重。通过案例分析,高温高尘SCR脱硝即使不影响预热器生产,也解决不了SCR反应器氨逃逸超标。高温高尘SCR脱硝项目采用4层催化剂都达不到氨逃逸达标,现在很多高温高尘SCR脱硝项目,为了节省成本,将催化剂简化为2层或3层,设计的催化剂还原比表面积就不够,这样SCR反应器氨逃逸更难达标。另外,中温中尘SCR脱硝和低温低尘SCR脱硝等不符合脱硝原理和常识的技术,更难实现SCR反应器氨逃逸达标。
为什么有些高温高尘SCR脱硝项目窑尾烟气检测氨气<8mg/Nm³?高温高尘SCR脱硝是实现不了SCR反应器氨逃逸达标。由于SCR反应器出口260~340℃的含氨气的烟气生料磨烘干生料过程,烟气温度降到110~150℃,进入窑尾袋除尘器,有50%以上气态氨被粉尘吸附后通过窑尾袋除尘器收集。另外,如果窑尾袋除尘器后端有湿法脱硫塔,湿法脱硫塔对氨气也有接近40%的脱除率。因此,少部分高温高尘SCR脱硝项目的SCR反应器逃逸的氨气<30mg/Nm³时,通过后端窑尾袋除尘器和湿法脱硫塔收集氨气,勉强可以实现窑尾烟气检测氨气<8mg/Nm³。大部分高温高尘SCR脱硝的SCR反应器出口氨逃逸严重超标,即使后端通过窑尾袋除尘器和湿法脱硫塔吸收部分氨气,有的氨气超过200mg/Nm³。
解决SCR脱硝氨逃逸达标只有采用高温低尘SCR脱硝通过水泥行业的SCR脱硝技术实践证明,高温低尘SCR脱硝是解决水泥脱硝最稳定可靠的技术。只有保证催化剂内孔干净,保证催化剂设计的有效催化还原的比表面积,让烟气中的NH3与NOx有足够催化还原条件,实现SCR反应器的氨逃逸达标或接近达标,再通过窑尾袋除尘器实现窑尾烟气氨气稳定达标排放。江西欣久为环保科技有限公司通过六年的时间,投资三千万研发成功的径滤式电除尘器,是不锈钢滤网除尘器和电除尘器的完美结合体,可以离线清灰。除尘效率高(达到90%) ,阻力小(小于200Pa) ,耐高温(达到550℃),取得六个国家专利证书。2024年在贵州资兆建材有限公司的高温低尘SCR脱硝项目,将预热器C1出口含尘100~130g/Nm³烟气通过径滤式电除尘器降到<6g/m³,再进入SCR反应器(采用20孔催化剂布置二层)。在6月22日通过有环保检测公司现场采样检测,各项指标全部达标,NOX为10~40mg/Nm³,氨逃逸为3~5mg/Nm³。另外,在预热器C1出口采用金属纤维毡滤袋收尘器除尘后实现高温微尘SCR脱硝技术也可以实现SCR反应器氨逃逸达标或接近达标。

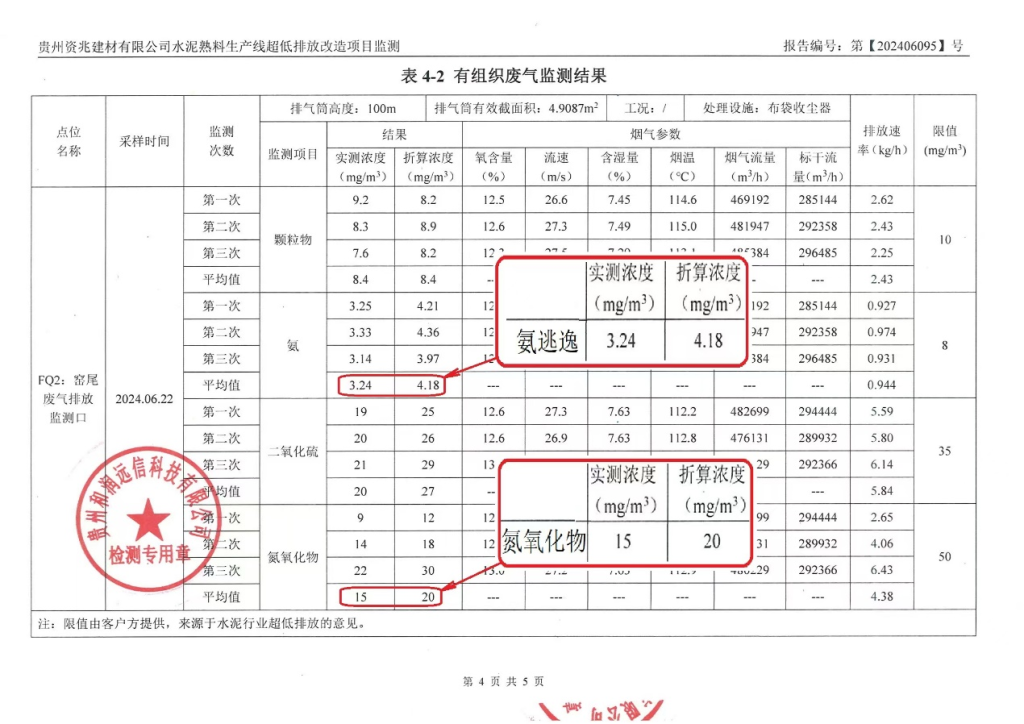
电石渣水泥窑采用高温低尘SCR脱硝可以实现氨逃逸达标电石渣水泥窑脱硝采用我公司的径滤式电除尘器在电石渣水泥窑的高温低尘SCR脱硝工艺流程,将电石渣水泥窑预热器C1出烟气口温度为480~680℃,将部分烟气通过余热锅炉或多管冷却器降温的烟气和没有降温烟气混合后,调节为350~400℃的烟气进入径滤式电除尘器,将150~190g/Nm3粉尘浓度降到6g/Nm³以内,再进入SCR反应器脱硝,脱硝后的340~390℃的烟气进入烘干生料破,烘干的生料通过旋风筒和窑尾除尘器收集,干净的烟气降低到110~130℃,再通过窑尾风机和烟囱排放。径滤式电除尘器收集的粉尘通过新安装的高温提升机送到预热器C3,实现预热器升级,节能降耗提产。该SCR脱硝工艺氨逃逸可以达标,即使后端烟气烘干破碎电石渣会释放少量氨气,由于烟气中的水分较大,窑尾袋除尘器可以起到半干法氨气吸收器的功能,有80%以上气态氨被粉尘吸附后通过窑尾袋除尘器收集,也可以实现窑尾烟气氨氨逃逸达标排放。
现有的大部分SCR脱硝项目因为氨逃逸超标需要推倒重来国内近三百多家水泥企业已经安装高温高尘SCR脱硝,正在建设和招标的SCR脱硝项目大部分还是选择高温高尘SCR技术。这些采用简易的高温高尘SCR脱硝技术大部分需要改造升级为高温低尘SCR技术,才能稳定实现氨逃逸达标。希望还没有安装SCR脱硝的水泥企业,选择合理可靠的高温低尘SCR脱硝技术线路,一次改造成功,避免后期升级改造,难度大,二次投资费用高。技术咨询联系电话:肖寒卫13908092823