目前,我国是全世界拥有最多万吨级水泥生产线的国家。随着严禁“两高”项目盲目上马政策日益收紧以及各地区产能置换要求愈加严苛,万吨线以后必然是越来越“稀缺”。而现有的万吨线项目在如此严格的政策环境下,究竟是如何高质量地进行生产发展的呢?
冀东水泥铜川万吨线
去年6月28日点火的冀东水泥铜川万吨线总投资约20亿元,是金隅集团首条日产万吨超低能耗、超低排放的熟料水泥国家级示范生产线。项目突出绿色、智能两大理念建设:
利用国内外最先进的二代新型干法熟料水泥生产线技术与装备,建成了一个低能耗、低排放和同步规划实施危险废弃物处理系统的“花园式工厂”,使氮氧化物、二氧化硫排放分别下降70%和80%,推动高排放企业向环保型企业转型升级。同时能处置城市发展中产生的多类固废、危废,助推铜川打造“无废城市”。
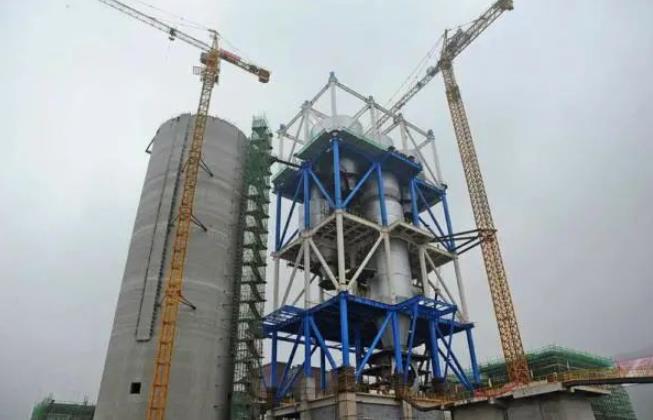
通过“5G+工业互联网”、大数据融合应用,打造工厂‘智慧大脑’,实现生产设备巡检、样品安全质量检测、矿山测绘等无人化、数字化管理运行,使劳动生产率、能耗利用率较传统水泥企业大幅提升。
海螺水泥池州万吨线
2020年4月15日,池州市政府与安徽池州海螺水泥股份有限公司签订了池州海螺四期项目合作协议。项目总体规划2条日产10000吨新型干法水泥熟料生产线,一次规划,分期实施,计划投资50亿元。一期建设一条万吨熟料生产线,配套18兆瓦余热发电,计划2022年上半年点火投产。万吨线建成投产后,安徽池州海螺水泥股份有限公司将成为全球规模最大的单一工厂。
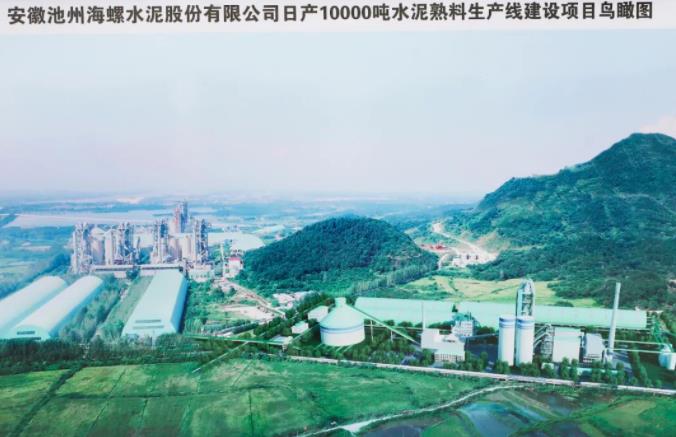
这条万吨生产线集成了专家操作系统、质量控制系统、智能辅助巡检系统等,同时后期在生产线上嫁接了最先进的替代燃料技术、富氧燃烧技术、水泥窑烟气二氧化碳捕集技术。通过这些技术的加持,能够保证万吨线绿色环保、经济、智能化,成为世界一流的生产线。
华新水泥黄石阳新万吨线
项目总投资30亿元,于2020年12月28日正式投产,采取公司自主研发制造的国内最大回转窑,配置30兆瓦的纯低温热发电和日处理3000吨生活垃圾衍生燃料的环保处理系统。2021年处理了生活垃圾108万吨,减排二氧化碳46.7万吨。计算下来,靠“卖碳”就可获利2300多万元。
华新水泥万吨线智能工厂项目通过应用智能行车系统、设备智能巡检系统、智能质量管控系统、水泥先进过程控制系统APC、数字一体化系统等,实现水泥生产全过程的数字化、可视化和智能化。通过营销数字化、智慧采购、智慧物流平台等系统,实现企业运营的数字化闭环管理。水泥综合能耗平均下降约4%,营销数字化平台销量占比高达95%以上,降低采购综合成本10%~20%,物流效率提升近50%。
尧柏水泥铜川万吨线
尧柏水泥铜川万吨线是全球最先进的第二代新型干法水泥生产线,总投资30亿。该生产线主要生产高性能混凝土、3D打印建筑材料、装配式建筑等九大业务板块,摒弃高能耗、高排放、高污染的传统落后产能和技术,突出智能化、绿色化、节约化三大优势。全力打造数字化工厂无人车间,超低排放,达到国家A级能效排放标准;利用余热发电,进行垃圾危废循环处理,预计投产运行后年发电量达到1.02亿度,减少二氧化碳排放9.05万吨,折合标准煤3.63万吨。
如此看下来,这些万吨生产线的建设发展不外乎这两个关键词:绿色化和智能化。其实对于整个水泥行业来说,未来的发展趋势都始终要围绕这两大主题,缺一不可。
绿色化
水泥作为传统优势产业,是碳减排的重点也是难点。除了做好淘汰落后产能的“瘦身”,也要在超低排放上下功夫。
加大投入采用先进技术,提高水泥窑协同处置生产线比例;加强清洁能源原燃料替代,大力发展光伏、风能、生物质等可再生能源;运用成熟稳定高效的脱硫、脱硝、除尘技术及装备,推动水泥行业全流程、全环节超低排放。
智能化
发展工业互联网、推进智能制造、扩展5G应用……聚焦推动制造业优化升级,“十四五”期间国家做出了一系列部署。
水泥企业建设智能化工厂,采用无人驾驶、智能装车等技术,能够节省人工、节约成本,在规避用工风险的同时,提高生产效率。对生产线进行智能化实时监控,能使熟料能耗指标大幅优化,是实现“双碳”的重要途径。
水泥企业应当从生产、管理、运输等各方面,运用新技术、新手段、新理念,不断探索新的智能化建设,实现企业生产全流程的数字化智能化发展。
国家双碳政策的收紧、燃材料价格上涨、产能过剩导致的市场竞争加剧等多重压力,促使整个水泥行业直面全新挑战,企业必须向着智能化、绿色化的方向转型。从万吨生产线广泛布局,到智能化工厂概念的普及,再到推动产业链高质量发展,都对水泥企业提出了更高的要求。想要可持续健康发展,必须抓住绿色环保和数字智能的风口,才能完美转型。