近年来,江西水泥所属泰和南方紧紧围绕“提质增效、优化升级”两大攻坚战,聚焦主业,做强水泥、做优商混、做大骨料,打出转型升级“组合拳”,积极推进“水泥+”,成为江西水泥第一家集水泥、商混、骨料生产销售一体化全能工厂,争做江西水泥“一体化”发展蓝图的践行者。
“水泥+”一体化 优化升级添动力
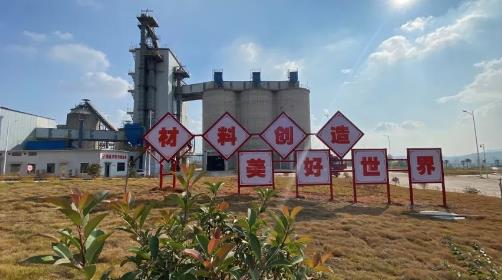
泰和南方原有的水泥、混凝土生产线产能规模小、工艺技术落后,经营发展面临巨大挑战。江西水泥审时度势,推行“一体化管理,协同化经营”经营新思路,开启了泰和南方成长壮大新征程。
2020年,积极响应泰和县政府“倍增计划”,全面推进“水泥+”发展战略,“水泥+”改扩建项目列入泰和县重点项目。当年8月,HZS180商混生产线新增建设和旧线环保技改实现并线运行生产。2021年11月,年产100万吨骨料生产线建成投产,标志着泰和南方以水泥销售为基础、以商混经营为抓手、以骨料生产为支撑的“一体化管理、协同化经营”格局正式形成。
“两翼”发展同风起。泰和南方积极贯彻中国建材“做强水泥、做优商混、做大骨料”的发展原则,项目建设快速推进,技术创新持续提高,破茧成蝶,迎风逆行,向阳而生,坚定地迈出了“一体化”发展之路。
生产一体化 管理整合提效率
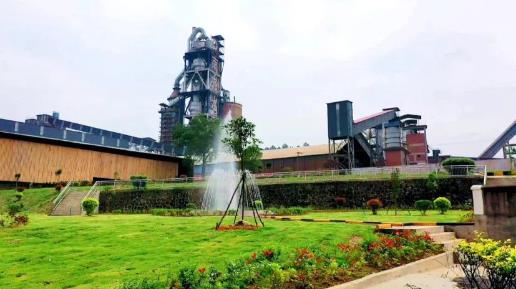
为推进瘦身健体、提质增效,实现高质量发展,泰和南方实施水泥、商混业务法人合并,人、财、物,产、供、销实行一体化管理,做到工作同谋划、同布置、同检查。
生产管理全面整合。将水泥、熟料、骨料、商混生产合并到制造部统一管理,生产组织、安全环保、质量控制实行管理统筹,各工段、各岗位统筹安排,有序衔接。针对水泥粉磨、商混、骨料生产在同一厂区的现状,项目设计时综合考量,实现水泥粉磨、骨料生产集中控制,骨料、商混产品同步检验,维修、机电队伍技术共享,优化了流程,减少了人员,为降本增效奠定了基础。
技术力量全力保障。骨料投产伊始,为尽快达产达标,不断调整摸索,攻关突破。生产技术上,采取了增长锤式破碎机的锤头,调整锤式破碎机锤头与筛板的间隙,改进高频筛内筛板等措施;产品质量上,源头控制砂石来料质量,改造配置机制砂喷水搅拌系统,配备专人进行骨料成品检测,骨料线投产三个月实现达产达标,台产提高57%,电耗下降65%,迈出了降本增效坚实步伐。
生产调度全程衔接。泰和南方骨料主要产品有骨料、机制砂、石粉三大类,占比不一,产品共生。由于库容小,一种产品滞销将因涨库影响生产连续性,产销衔接成为骨料连续生产的制约因素。泰和南方成立产销调度中心,每日根据客户骨料品种需求提前上报调度中心,生产部门根据品种做到合理安排,同时辅以水泥窑生料配料和搅拌站骨料自用。骨料生产消化矿山废石,水泥生产消化骨料副产品,商混生产消化骨料和水泥产品,实现了水泥、商混、骨料生产循环联动,优化了库存空间,保障了生产连续高效运行。
经营一体化 创新营销增效益
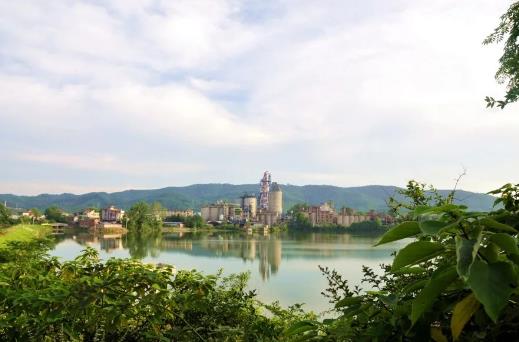
泰和南方作为江西水泥第一家全产业链公司,先行先试,坚持走一体化道路,不断创新营销模式,凸显“市场一体化”经营理念,整合水泥、商混、骨料销售及供应链渠道,打造综合性经销商,做到资源共享,信息互通,市场共建。以商混销售为杠杆,带动水泥和骨料销售提升,让一体化管理的成本优势,全产业链带来的协同优势,在市场上充分展现为高话语权和强竞争力,真正形成“以水泥销售为基础,以商混经营为抓手,以骨料生产为支撑”的“一核两翼”一体化经营格局,为江西水泥一体化管理贡献“泰和方案”。
骨料销售方面,细分产品定位,确立了以泰和、吉安为核心区域,按照“先拌站、再工程、后网点”思路,以持续互惠互利、合作共赢、同谋发展的战略布局,“精准销售”抢市场,骨料销售创佳绩,2022年首年投放市场即达产达标,骨料外销及商混自用产能发挥率达108%。
商混销售方面,确立“抓大不放小,就近不舍远”、“攻关抢占城区方量,巩固提升乡镇方量”策略,市场占有率由原来不足8%提高升到39%,2019年至2022年,商混销量、净利润逐年大幅增长,“1+1>2”的效果初步显现。创新营销模式,由传统直销垫资销售调整为直销、经销、代理多形式销售,有效防患了资金风险,改善了商混经营质量。
商混销售助力骨料、水泥拓市场,为水泥主业赢得市场提供有力保障,一核两翼,齐头并进,联动创效优势已经显现,一体化的竞争优势在市场上也得到了很好的印证,G105泰和县文田至上田立交桥段公路改建工程是一体化协同创效的典范,整个工程商混、水泥、骨料全部使用公司产品。“市场一体化”实现了板块协同发展,为公司经营效益完成形成强大支撑。
万里长风起云端。泰和南方“一体化”发展蓝图已经绘就,泰和南方将坚持以党的二十大精神为引领,全面贯彻新发展理念,坚定不移走高质量发展之路,助力江西水泥实现“2255”高质量发展目标,为新天山水泥建成具有中国特色的世界一流水泥公司作出新贡献。
来源:江西水泥