近日,安徽省池州市经信局发布消息,2月18日,池州海螺水泥四期项目—日产10000吨新型干法水泥熟料生产线顺利完成省经信厅产能核验。
池州海螺水泥万吨线自2020年12月5日开工以来,在池州市政府的支持和专业部室的共同努力下,在集团、股份公司各级领导的高度重视和悉心关怀下,积极克服疫情等不利影响,奋战高温酷暑,紧紧围绕项目点火投产目标,各项节点计划有序推进。项目建设秉承“生态优先、智能控制、指标先进、节能环保”的指导思想,系统总结海螺及国内外特大型生产线最新科技成果,邀请世界级的装备厂家进行技术装备配置,优先选用节能环保材料,大胆使用“四新”技术,预分解系统选用双系列低压损五级预热器和高效低氮分解炉,原料粉磨系统采用“V选+辊压机+动选”的高效设备组合。
该生产线投产后,吨熟料煤耗、综合电耗等经济技术指标,氮氧化物排放等节能环保指标,系统智能化程度等都将达到世界先进水平,预计可实现年平均营业收入10亿元以上。万吨线的建成投产,标志着池州海螺成为世界最大单一水泥熟料生产基地,将为池州市“十四五”期间实现高质量发展提供重要支撑和强劲动力。
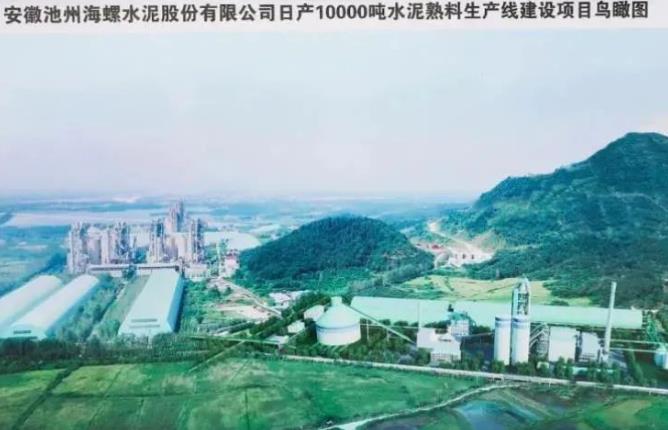
据智慧水泥了解,2000年海螺正式落户池州。池州作为海螺水泥的重要阵地,到目前为止,海螺累计在池投资超过70亿元,建成6条日产5000吨、1条日产8000吨熟料生产线,水泥熟料产能达到1680万吨,累计上缴税费73亿元。池州海螺四期项目,是海螺集团利用新技术、新装备投资建设建材产业链转型发展项目。
该项目是安徽池州海螺四期日产10000吨水泥熟料生产线项目,总体规划建设2条日产10000吨新型干法水泥熟料生产线,并配套建设440万吨/年水泥粉磨站。一期项目于2020年12月5日在贵池区牛头山镇正式开工建设。此条万吨线建成后, 池州海螺熟料产能将达1900万吨,成为世界最大单一水泥熟料生产基地,在生态保护、节能减排、智能化水平方面可代表全球最先进水平,势必会为海螺水泥在市场中再添重要一笔,影响整个长三角和长江沿线地区水泥市场。
据智慧水泥统计,目前我国水泥万吨线有17条,是全世界拥有最多万吨级水泥生产线的国家。
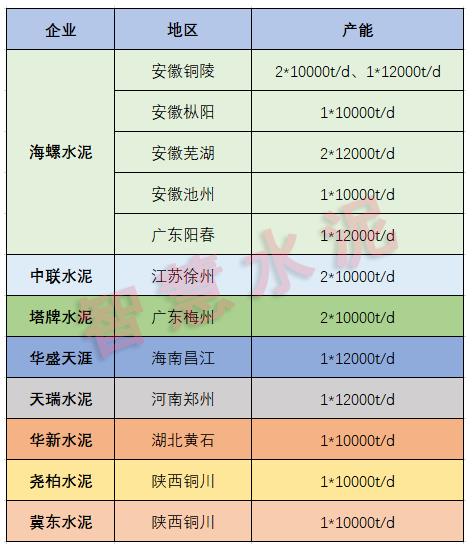
在严控两高项目盲目发展、产能置换政策持续收紧的背景下,未来再增加新的万吨线可以说会越来越难。此前,江苏省工信厅对2021年8月5日公示的溧阳市前峰水泥有限公司搬迁建设2条10000t/d水泥熟料生产线方案予以撤销,撤销原因为:常州溧阳市东方水泥有限公司因经营原因于2017年停业关闭,相关生产许可证于2018年过期。但溧阳市工业和信息化局2021年上报不实材料,称该企业因规划调整而停产搬迁,符合迁建条件,计划异地新建水泥熟料生产线。省工业和信息化厅审核把关不严,同意迁建方案并发布公告。
目前,我国水泥行业产能过剩的局面依然存在,激烈的市场竞争给企业带来巨大的压力。想要在市场中稳固立足,不能盲目追求产能却忽视了制造水平。我国水泥万吨线不仅产能大,而且都通过大量资金和技术投入,在绿色环保、智能发展等方面均达到世界领先水平。
冀东水泥万吨线项目总投资约20亿元,配套建设杨泉山矿山,15兆瓦纯低温余热发电系统,水泥粉磨及发运系统、脱硫系统和脱硝系统;协同处置工业固废、危废。建成了一个低能耗、低排放和同步规划实施危险废弃物处理系统的花园式工厂,氮氧化物、二氧化硫排放分别下降70%和80%,推动高排放企业向环保型企业转型升级。
尧柏水泥万吨线采用第二代新型干法生产工艺,配套建设有15WM纯低温余热发电系统及年处置规模20万吨固废危废项目,是西部地区首条智能化万吨示范生产线,也是尧柏发展史上技术最为先进、环保水平最高、建设标准最高的生产线。
华新水泥基于阿里云工业控制优化平台AICS,搭建出水泥低碳制造智能先进控制系统HIAC,成功实现了大规模环保协同处置时的工况稳定控制,进一步提升了燃煤替代率与质量稳定性。在公认控制难度最高的黄石“万吨线”,新系统使得煤的替代率最高达38.3%,实现全年再减碳6万余吨。于近日通过了中国建筑材料联合会的鉴定,被认定为“整体技术达到国际领先水平”。
天瑞集团郑州水泥有限公司的万吨线是由天瑞集团投资建设的世界上第一条日产12000新型干法熟料生产线,年产优质熟料400万吨、水泥500万吨,并配套18MW纯低温余热发电机组和年产600万吨骨料生产线,实现余热和排废矿石的回收再利用。该生产线采用中央集中控制系统,全部自动化操作,核心设备均从国外引进,是世界上第一条单线生产能力最大、技术装备最先进的绿色环保生产线。
如此看下来,这些万吨生产线的建设发展不外乎这两个关键词:绿色化和智能化。其实对于整个水泥行业来说,未来的发展趋势都始终要围绕这两大主题,缺一不可。
绿色化
水泥作为传统优势产业,是碳减排的重点也是难点。除了做好淘汰落后产能的“瘦身”,也要在超低排放上下功夫。
加大投入采用先进技术,提高水泥窑协同处置生产线比例;加强清洁能源原燃料替代,大力发展光伏、风能、生物质等可再生能源;运用成熟稳定高效的脱硫、脱硝、除尘技术及装备,推动水泥行业全流程、全环节超低排放。
智能化
发展工业互联网、推进智能制造、扩展5G应用……聚焦推动制造业优化升级,“十四五”期间国家做出了一系列部署。
水泥企业建设智能化工厂,采用无人驾驶、智能装车等技术,能够节省人工、节约成本,在规避用工风险的同时,提高生产效率。对生产线进行智能化实时监控,能使熟料能耗指标大幅优化,是实现“双碳”的重要途径。
水泥企业应当从生产、管理、运输等各方面,运用新技术、新手段、新理念,不断探索新的智能化建设,实现企业生产全流程的数字化智能化发展。
国家双碳政策的收紧、燃材料价格上涨、产能过剩导致的市场竞争加剧等多重压力,促使整个水泥行业直面全新挑战,企业必须向着智能化、绿色化的方向转型。从万吨生产线广泛布局,到智能化工厂概念的普及,再到推动产业链高质量发展,都对水泥企业提出了更高的要求。想要可持续健康发展,必须抓住绿色环保和数字智能的风口,才能完美转型。